Global Plastic Crisis: Challenges and Recycling Solutions
- Share
- Issue Time
- Apr 1,2025
Summary
Plastic pollution has become a global environmental crisis!
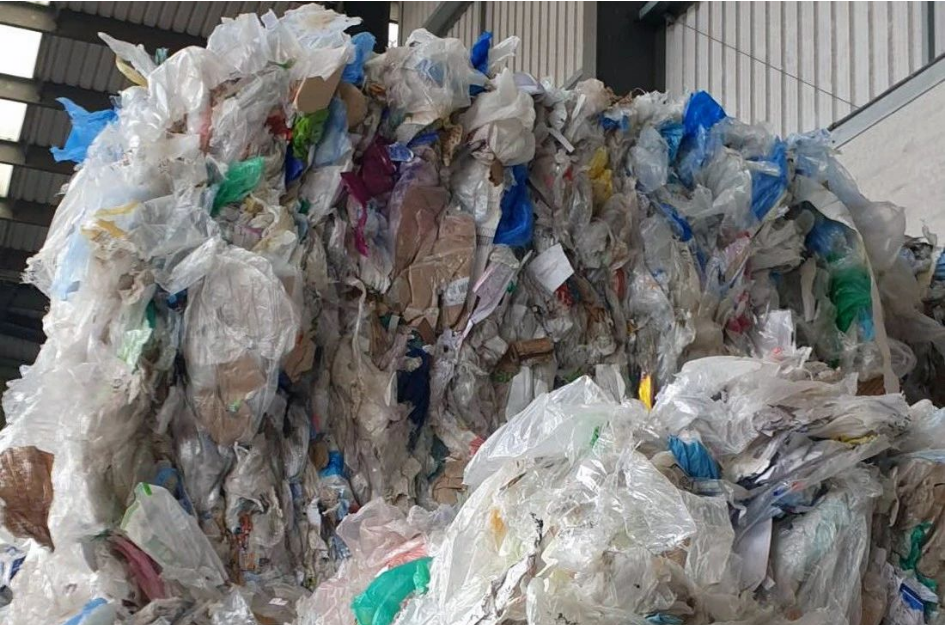
Data from the UN Environment Programme reveals that one million plastic bottles are sold every minute worldwide, while approximately 40 million tons of plastic waste enter the oceans annually, equivalent to dumping a truckload of garbage into the sea every minute. Plastic pollution has become a global environmental crisis!
I. The Challenges of Plastic Recycling
Plastic recycling is often termed the "most complex waste sorting challenge."
Material complexity: Among 60 million tons of plastic waste, there are over 10 types of materials (e.g., PET, PE, PP), varying in size, melting points, and densities, making sorting extremely difficult.
Value: Over 40% of waste consists of low-value plastics like packaging films and bags. High recycling costs and low profitability often lead to landfilling or incineration, wasting most of their potential value.
II. Main Plastic Recycling Methods
Three primary approaches exist: mechanical recycling, chemical recycling, and energy recovery.
Mechanical Recycling
Principle: shredding → washing → melting → reprocessing into pellets or plastic products.
Pros: Mature technology, low cost (accounts for 90% of global recycling).
Cons: Limited to single-material streams (e.g., PET bottles, PE films). Each recycling cycle degrades quality (e.g., water bottle → textile fiber → carpet), reducing value.
Case study: 1 ton of plastic bottles yields 900 kg of recycled fiber, saving 6.2 barrels of oil.
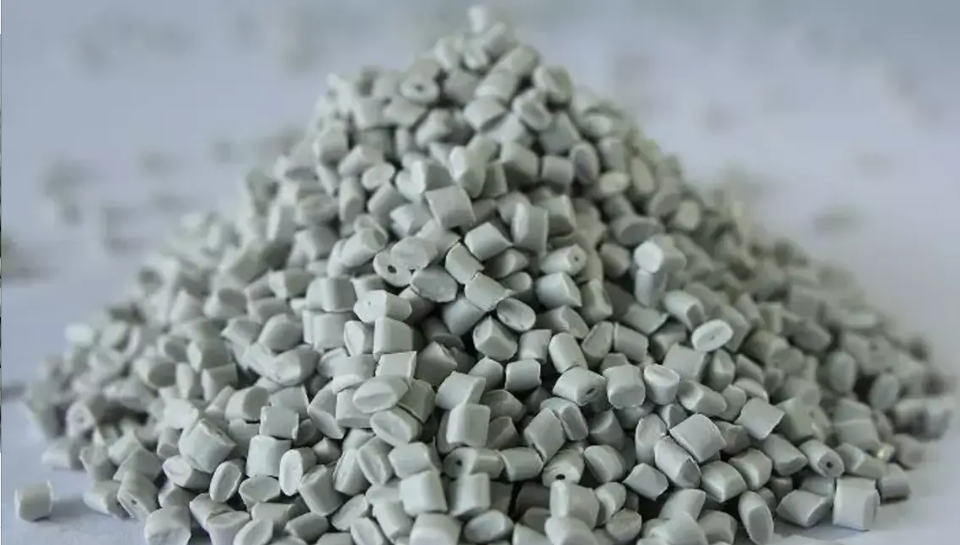
Chemical Recycling
Principle: shredding + sorting → depolymerization (pyrolysis/hydrolysis) to extract monomer feedstock.
Pros: Handles mixed/low-value plastics (e.g., agricultural film, paper mill waste).
Cons: Energy-intensive; costs 3× higher than mechanical recycling.
Case study: Enables closed-loop recycling, enhancing plastic’s economic value.
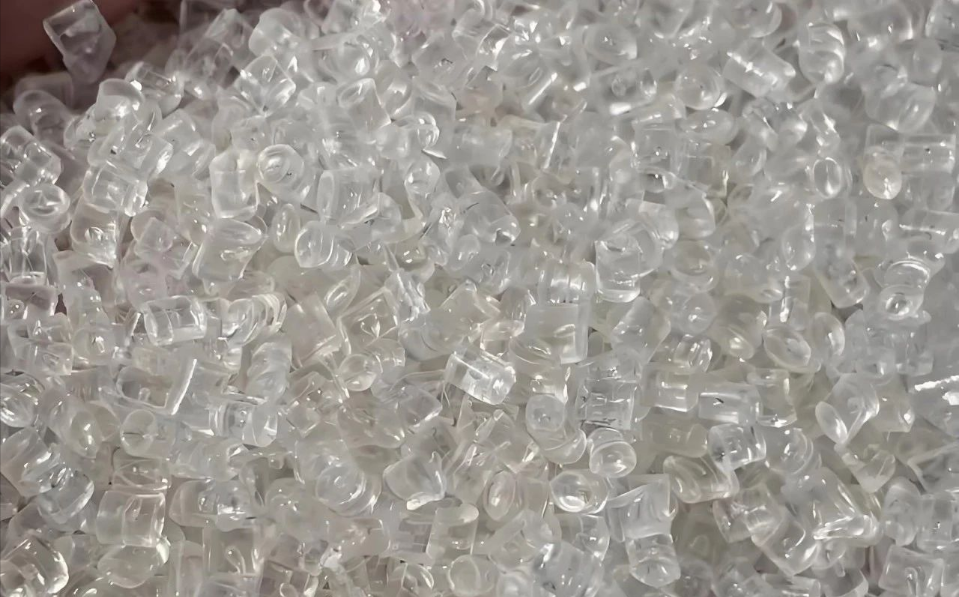
Energy Recovery
Principle: Crushing + screening to produce RDF (refuse-derived fuel) for cement kilns/power plants (calorific value: 5,000–6,000 kcal/kg).
Pros: 90% volume reduction; suitable for non-recyclable plastics.
Cons: CO₂ emissions require flue gas treatment (e.g., desulfurization/denitrification).
Case study: Japan derives 3% of its electricity from plastic incineration but pays environmental taxes.
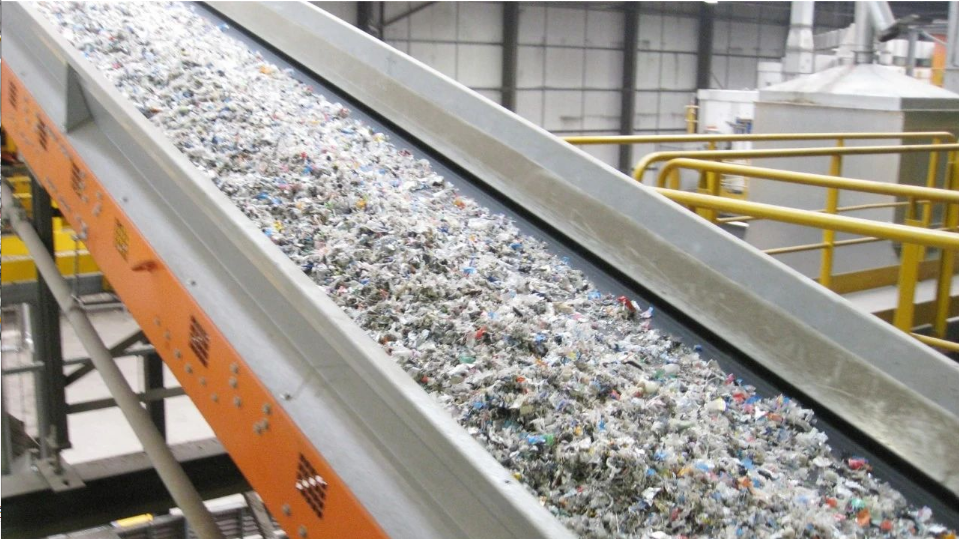
III. The Key to Recycling: Pre-Shredding
All three methods require a critical pre-processing step—crushing—whose quality determines downstream success.
Purpose: Converts bulky, irregular waste (films, pipes, bottles) into uniform particles for washing, separation, and reprocessing.
Challenges:
Variations in hardness/toughness (PET vs. PE vs. PP) and contaminants (metal, sand) cause jamming and inefficiency in traditional equipment.
Over-crushing by high-speed shredders increases material loss and pollution.
Solution: Industrial-grade single-shaft shredders are revolutionizing pre-processing.

1. Intelligent Feeding & Shear Gap
Curved pressurizing device boosts cutting efficiency and throughput.
Special alloy blades (heat-treated for hardness) shred engineering plastics (ABS, PC) with lower wear cost per ton.
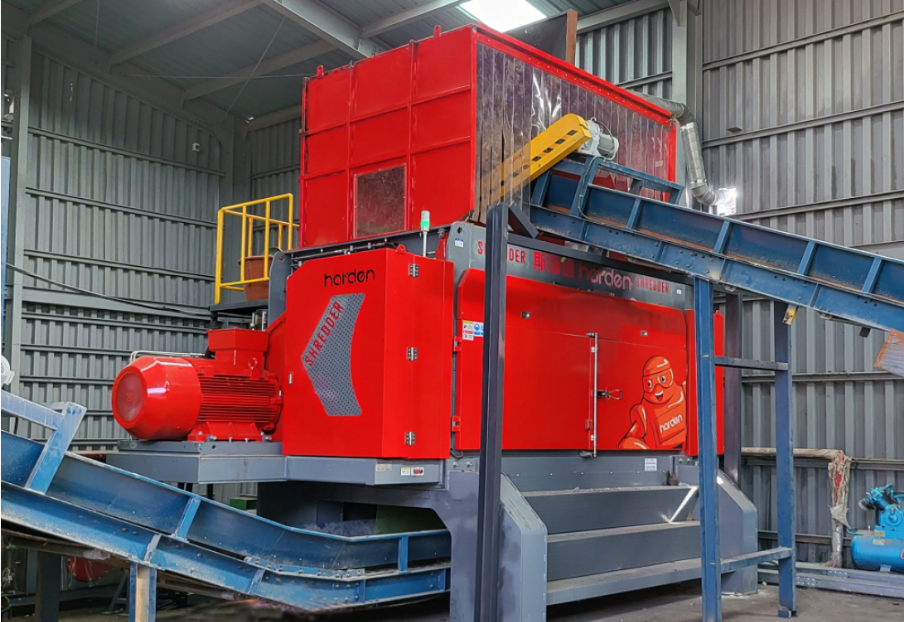
2. Precise Particle Control
Customized output (20–100 mm), ideal for all recycling paths.
Quick-change screen design adapts to varied materials.
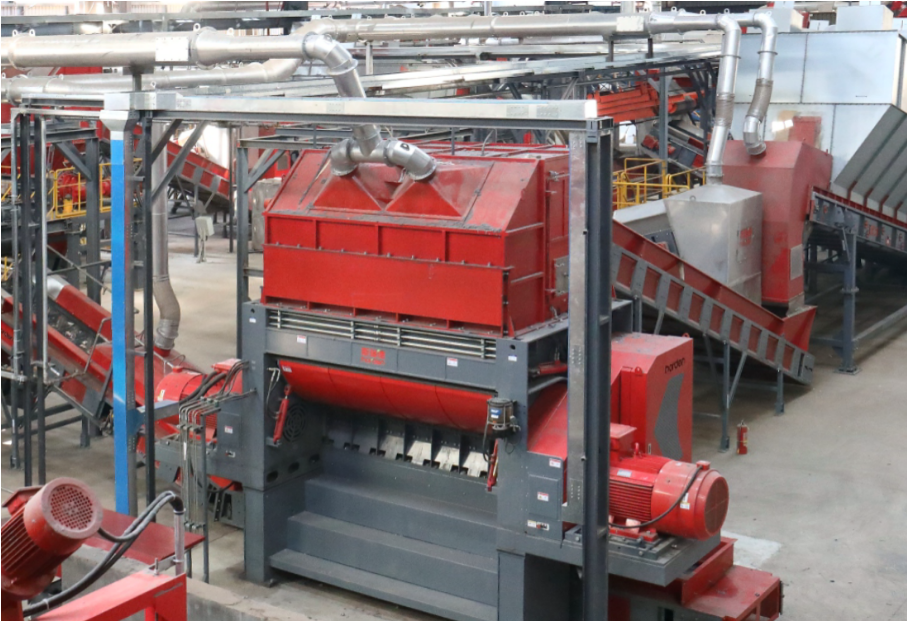
3. Energy Efficiency & Stability
Medium RPM reduces power use; smart control + CE safety systems ensure reliable operation.
400+ global projects; preset programs for 2–30 t/h output across waste types.
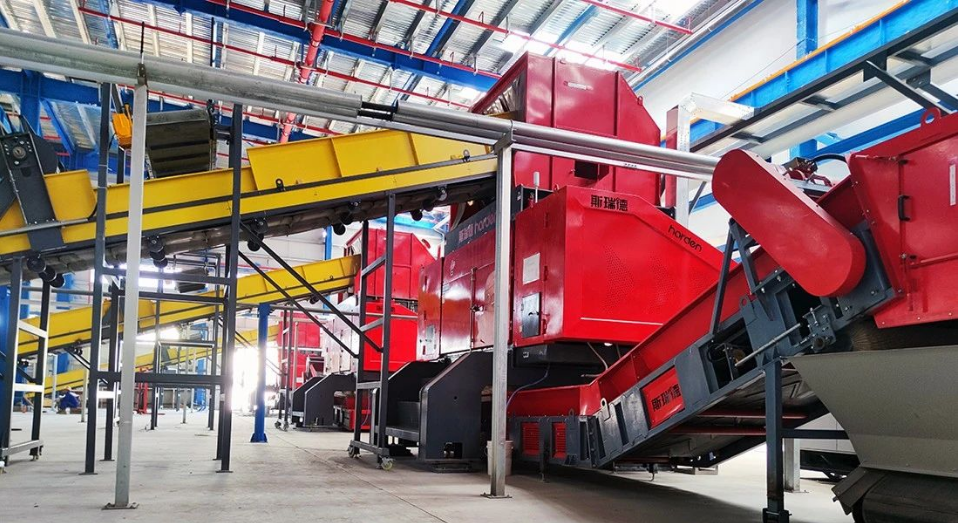
4. Applications
Films/bags/bottles: 3–5× denser output cuts transport costs, ready for chemical recycling.
Pipes/rigid scraps: Directly shreds large PE pipes/hard plastics without pre-cutting.
Mixed waste-to-RDF: Converts waste into high-quality fuel for kilns/boilers, replacing fossil fuels.
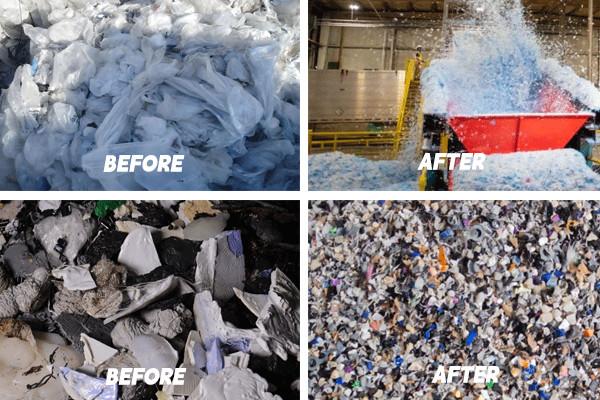
Conclusion
The future of plastic recycling starts with effective crushing. HARDEN’s single-shaft shredder is the linchpin of circular economy—transforming China from a "plastic giant" to a "green manufacturing leader" through innovation and scale.